Sinker EDM, also referred to as Ram EDM, uses electrodes machined from graphite or copper to shape the workpiece. Typically found in die/mold component manufacturing, a Sinker EDM raises and lowers (sinks) the electrode along the workpiece.
Regardless of the name you use, this method relies on the same thermal erosion process found in electrical discharge machining to shape a workpiece. What’s different in Sinker EDM is how a shaped tool becomes the electrode through which large amounts of electricity are discharged. The electrode is machined out of graphite or copper material into a negative or the reverse version of the cavities and contours designed into the workpiece.
Details produced with the Sinker EDM process can be either a through cavity or blind cavity. The prepared electrode is always the negative or inverse shape of the final detail. Electrodes are typically manufactured by milling, but can be also be machined with Wire EDM depending on geometry detail. Normal electrode sizes can range from under 1.0” square to 6.0” square, but can be larger. All machining is performed submerged under a special dielectric oil. Oil is used as a dielectric due to the higher power levels achieved by the larger sized electrodes. Machine programs are typically created on the machine, but some specialized off-line Sinker EDM CAM systems do exist that utilize available 3D CAD model information of the workpiece and electrodes for programming.
Graphite and copper are the most common electrode material types. Graphite usually provides the best economy, easier electrode manufacturing, and also delivers the fastest Sinker EDM machining speeds. There are many different grades of graphite, with each one being designed for a specific application or price point. The most notable graphite grade differences are in the grain structure size of the material. Copper electrodes will produce the best surface finishes in Sinker EDM, and copper tungsten is used for the EDMing of carbide.
In the past, many Sinker EDM operations used external flushing to help evacuate debris from the spark gap. Today’s machines use what is called “no flush” technology, but a form of flushing is still used. Rather than using external flush hoses, the Z-Axis head (RAM) holding the electrode is rapidly raised and lowered, creating a hydraulic effect that pushes and pulls debris out from the spark gap area. To achieve faster machining rates, a rough and finish electrode are usually made, each having a different undersize amount to accommodate differences in the overburn values for the power settings used. Different electrode orbit patterns are used to achieve final part size and accuracy.
Sinker EDM machines can be equipped with automatic tool changers to enable long, unattended run times. Multiple electrodes then can be used for roughing and finishing operations. These machines also can be loaded and unloaded with fixtured workpieces in robotic cells to increase productivity by maximizing unattended operation.
Stay Tuned for More!
If you’ve enjoyed lesson four in this 6-part Back to Basics series, be sure to stay tuned for future lessons as we reflect on our industry and celebrate the building blocks that have led us to the fascinating EDM advancements that we encounter each day.
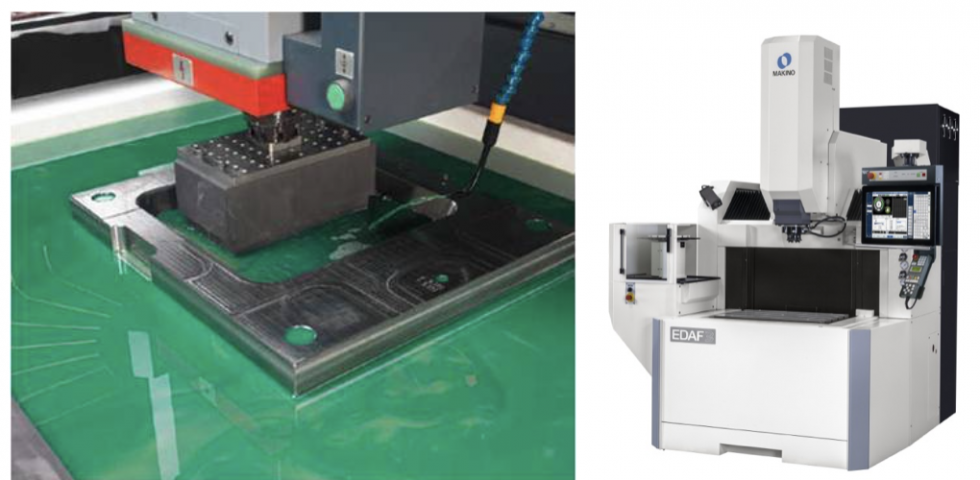