This is a great question that applies to both plain brass and coated wires. When comparing wires, several characteristics and attributes should be examined, especially when trying the first spool of a new wire brand or type. Price alone is not a good gauge.
Depending on how often you buy different brands or types of wire, it may be beneficial to establish a few baseline evaluation tests. Some observations may require longer-term testing over multiple spools to establish the impact they might have on overall production and reliability.
4 Main Wire Characteristics
- Cleanliness
- Wire memory and threading capabilities
- Cutting performance
- Variation of the wire by batch
In this first of two posts, we’re going to look at the first two characteristics: EDM wire cleanliness and wire memory.
Cleanliness: This can be a challenging item to observe, and may introduce a level of speculation. On machines with felt pads, using a new set or location on the felt pad wipers is a great way to determine how clean or dirty a wire might be. You’ll need to establish a baseline with the current wire being used; an evaluation of the felt pads after 20-40 hours of operation will be sufficient. Wire that is deemed “dirty” will typically show signs of greasiness or wire flaking on the felt pads or machine rollers. Dirtier wires can also yield shorter life on power feed contacts, and more frequent machine maintenance intervals may be necessary to ensure system reliability.
A simple, but not scientific, way to determine cleanliness is to pull a tissue like Kleenex down a specific length of unspooled wire. Typically, 20 feet should be enough to at least get a rough impression.
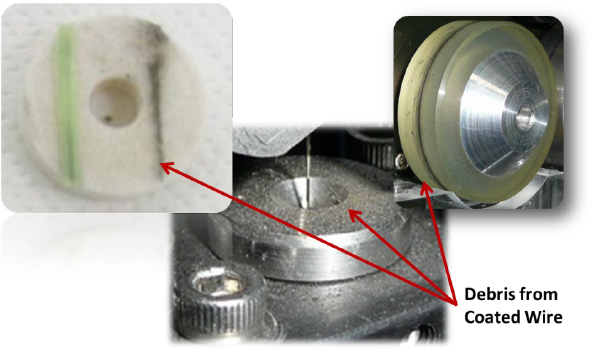
Wire Threading Reliability / Wire Memory: This test is straightforward to perform and evaluate. Using the preferred AWT (Automatic Wire Threading) mode setting (preferably High Speed), verify that the wire can reliably be automatically threaded at various heights. If a wire has excessive memory (the wire wants to curl back up as it comes off the spool), it can cause wire threading reliability issues as the wire wants to curl out of the threading jet. It’s also helpful to verify the wire as it exits the rear pinch rollers, especially after Rough Cut machining. Wire that has excessive memory will not want to lie flat in the spent wire bin, and may cause issues with machines equipped with Wire Choppers. An easy test is to cut a 1.5 meter (60”) length of wire, and hold it vertically. There should not be any more than (x2) crests or waves in the wire over a 1 meter (36”) length, and the crests should not exceed 40mm (1.6”) in size.
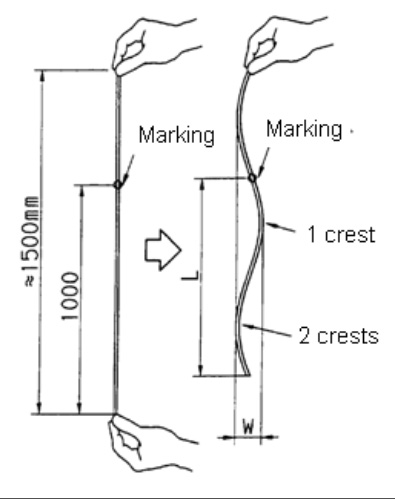