Angular start holes commonly occur when machining mold tooling lifter pockets and ejector pin details. As part of this process, a position for manual wire threading needs to be determined within the profile, and a M01 Stop Point should be created within the NC program. When processing with a tapered start hole, the angular start hole position needs to become part of the program, so it’s included within the program’s cutter compensation (G41/G42) line.
If the angular start hole location is not part of the cutter compensation (G41/G42) movement, a machine alarm can occur. In the case of 4-axis programs, cutter compensation may not be activated properly if the U/V axes are not vertical, leading to improper size and location. Depending on the CAM system’s output and options, some manual editing of the program may be required, but the overall changes will be minimal.
It is possible to create programs with angular start hole locations using “T” taper NC code or full 4-axis programs. As part of all U/V axis machining, the taper data information (program plane, sub-plane, and Z-position) must be properly set and can be programmed using the G95 statement. The images below show an example of a 15-degree angular hole in a workpiece with a height of 2.500 inches. A tapered start hole is necessary because the top and bottom profiles do not intersect the Z-plane top view. This example has been processed as a 4-axis program, and the standard program NC code and modified NC code for the tapered start hole has been provided.
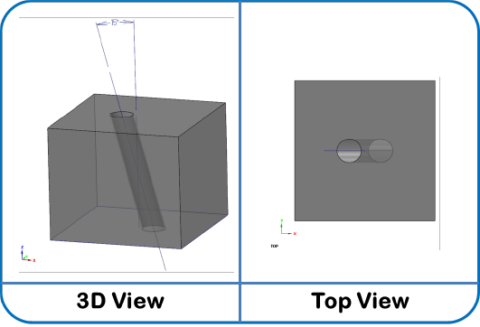